Las Vegas Clinical Laboratory UMC Prioritizes STAT Runs, Streamlines Through Consolidation
By automating clinical chemistry and immunoassay testing, clinical laboratory leaders can improve throughput while reducing the stress on staff, laboratory expert says
The American Society for Clinical Pathology regularly conducts a vacancy survey of medical laboratories throughout the US. While the problem of lab department vacancy rates has been ongoing, the last survey reported showed increased rates for laboratory positions across all departments surveyed. Last year, burnout among healthcare workers reached a crisis level, reported Clinical Laboratory News.
As a result, staffing the clinical laboratory with qualified lab professionals resounds as a top concern—and at a time when expectations are perhaps the highest they have ever been for performance in healthcare operations, from general hospitals to the most complex integrated delivery networks.
Even in the midst of the clinical laboratory workforce shortage and chronic strain, laboratory leaders must still improve their labs’ processes and workflows; increase productivity; and expand routine and specialty testing to better serve patient populations.
Faced with unrelenting pressures to do more with less, lab directors are turning to automating certain departments of the laboratory as a way to:
- Relieve the problems caused by an ongoing workforce shortage;
- Improve workflows and processes through standardization;
- Keep lab staff working on the most important tasks; and
- Enhance the laboratory’s reach and grow the lab business in necessary ways.
How UMC Southern Nevada Prioritized STAT Runs, Consolidated Operations
One case in point highlights the University Medical Center (UMC) of Southern Nevada’s clinical laboratory. Located in Las Vegas, UMC is among the largest public hospitals in the United States. It is part of a recent master-planned Las Vegas Medical District (LVMD), and it is the only Level I trauma center in Nevada.
The laboratory needed to improve turnaround time and expand the test menu, among other goals, explained Scott Keigley, one of two General Laboratory Services Managers at UMC. While limited laboratory automation had already been applied broadly, the lab took its automation initiative one step further by connecting three high-volume automated clinical chemistry and immunoassay analyzers (CC/IA), an automated hematology line, and a coagulation analyzer.
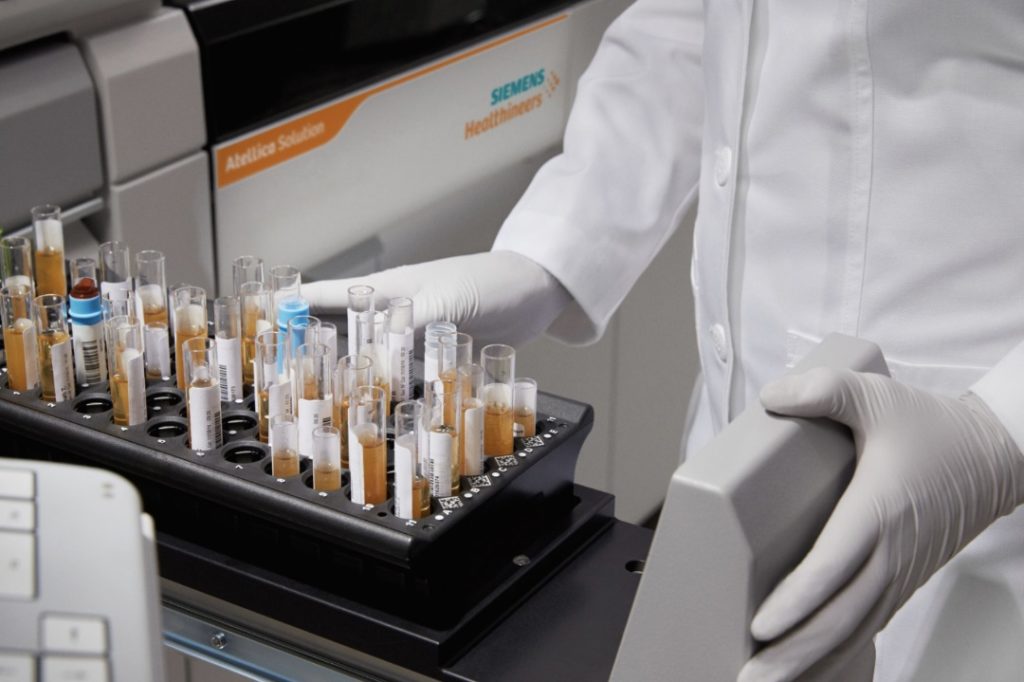
The University Medical Center of Southern Nevada improved efficiency and streamlined workflow by integrating a consolidated automated clinical chemistry and immunoassay analyzer (above) into the laboratory’s workflow. (Photo copyright: Siemens Healthineers)
An immediate benefit that UMC realized was consolidation of clinical lab operations. “Up until implementing our automated platform, we had a dedicated laboratory in our emergency room specifically to triage our emergency room tests,” Keigley explained. “You’re talking about not only a duplication of consumables, resources, and supplies, but also personnel.
“A big part of automating was showing our administration we were going to be able to eliminate that emergency room lab and still turn our results around as quickly and as efficiently without it,” Keigley added.
One of the ways that using an automated platform enabled consolidation of lab operations was by decreasing the turnaround times of STAT samples. “Our STAT turnaround times are way below many of the national thresholds or standards,” Keigley explained. “I’ll use troponin as an example. National threshold is 60 minutes from received to result, but we average about 30 minutes.
“Throughput definitely increased,” Keigley added, emphasizing that this increased throughput was actually accompanied by a reduced workload. “We’ve seen a reduction in the amount of hands-on time required to do the daily maintenance and quality controls. Once the daily maintenance and controls are completed, the chemistry department can usually be run by one person.”
Choosing a Consolidated Automated Chemistry and Immunoassay Platform
Described as flexible for adding components, modular, and scalable, a consolidated clinical chemistry and immunoassay analyzer (CC/IA) can run from 1 million to 3 million tests per year. Designed with innovative technological internal controls and sample handling—and other capabilities that include automated instrument calibration, maintenance, and quality control (QC) functions—the CC/IA platform also works as a standalone and is a first step toward implementing laboratory automation.
At UMC, multiple factors influenced the decision to add the platform, explained Keigley. “One reason was the increased productivity that it (the Atellica Solution) from Siemens Healthineers offers. This technology frees up our techs to do what we went to school to do. I can show anyone how to load samples on these analyzers in five minutes, but that’s not what it’s about.
“We were able to expand our test menu and our services. The platform allowed us to grow.” Keigley estimates that UMC’s test menu grew up to 20% after the change, both expanding the types of testing that could be offered and decreasing the number of send-outs. He estimates that the chemistry lab now processes about 2.6 million reportable results per year.
There were several (QC) features that Keigley believes UMC’s laboratory benefits from. The key QC features Keigley identified include onboard temperature-controlled storage, programmable run times, and barcode-labelled tube options from the control manufacturer that eliminate manual programming.
Operational Evaluation—Nexus Global Solutions, Inc. (Nexus), Plano, TX
While the primary driving factor in UMC’s decision to use the Atellica Solution platform was based on its individual laboratory’s needs, a recent study commissioned by Siemens Healthineers illustrated the benefits of this system.
An operational comparison report by Nexus found that there are multiple advantages associated with this integrated automation platform—as a standalone component—when compared to a similar offering.
Specifically, the Nexus report found:
- Start-up and maintenance time was almost an hour and a half less;
- Manual start-up time requirements were 28 minutes, compared to 46 minutes;
- From 65% to 69% of samples had a faster turnaround time; and
- A system footprint that used 20square feet less space and four fewer analyzers.
Clinical laboratory leaders can review the methodology and results of the Nexus Global report by clicking on this link: www.siemens-healthineers.com/operational.
This article was produced in partnership with Siemens Healthineers.
—Caleb Williams
Related Information:
Vacancy Survey of Medical Laboratories in the United States
University Medical Center of Southern Nevada