Top-performing medical laboratories are using Lean to help craft RFPs, evaluate TLA options, then implement the automated systems to achieve optimal quality and productivity
In recent years, there’s been a big change in how clinical laboratories purchase total laboratory automation (TLA) solutions, and then integrate this automation into their lab operations. Using a strategy that is somewhat off the radar, top-performing medical laboratories will purchase and install TLA only after applying the principles of Lean to the physical layout and overall workflow within their labs.
This development demonstrates the growing acceptance of Lean, Six Sigma, and continuous process improvement methods at hospital-based laboratories and independent clinical laboratories.
As lab budgets get squeezed down each year and specimen volume increases, pathologists and clinical lab managers face the twin challenges of reducing costs while increasing the quality of their lab testing services.
Why Top-Performing Medical Laboratories Use Both Lean and TLA
For these reasons, Lean methods are now integral to the use of laboratory automation among top-performing clinical laboratories. These labs use a new cycle for procurement and implementation of lab automation. Steps in this cycle involve Lean methods in the creation of the RFP (request for proposal), in the pre-purchase assessment of proposals, and in implementation, followed by the use of continuous improvement designed to extract maximum quality and optimal productivity from the laboratory automation installation.
When labs are incorporating Lean methods and a culture of quality management in their operations, they change the traditional steps they followed when preparing to replace an aging, outmoded system with a new one capable of revising almost all aspects of lab operations.
Forward-looking pathologists and clinical lab directors view the installation of a new automation system as an opportunity to revise not only the automated processes but also as many other lab operations as possible.
In fact, they view the challenge of implementing a new system as a chance to address almost all of the most challenging problems in laboratory management today. These problems range from:
- Reimbursement levels that have been declining for years and are expected to continue to decline;
- A shrinking lab workforce;
- An aging population with more chronic diseases;
- To the most pressing need of testing more specimens while delivering greater value simultaneously.
Manual Processing in Clinical Laboratories Is Subject to High Error Rates
“Among the benefits of both Lean and TLA is that labs can maximize efficiency and reduce errors simultaneously,” stated Joe Ross, Senior Marketing Manager, North America Automation and Clinical Informatics, for Beckman Coulter in Brea, Calif. “Lab managers recognized that any area of the clinical laboratory that involves manual processing is subject to high error rates. This is particularly true of the pre-analytical and post-analytical phases of the lab testing workflow that humans handle. It is these areas that generate the most benefits when a lab blends Lean with new lab automation.”

“In an environment saturated with total lab automation solutions to help improve quality, labs constrained by size and budget need to look for solutions to help reduce variation in manual processes—including both physical and decision-making processes. Utilizing Lean processing initiatives, which are designed to eliminate waste and improve efficiency in various processes and industries, is the first step toward identifying key areas for improvement,” stated Joe Ross (above), Senior Marketing Manager, Automation and Informatics, Beckman Coulter. (Photo and caption copyright: Clinical Lab Products Magazine.)
Other areas that benefit from both Lean and TLA are turnaround time. In general, Lean experts say, Lean labs can and should have an average TAT of less than 30 minutes. In addition, the combination of Lean and automation systems can help labs reduce variation in TAT as well.
One of the biggest challenges medical laboratories face is the ability to handle stat testing smoothly and efficiently. Lean management and the best in class automation systems can process stat tests in less than 30 minutes—meaning from the time the lab receives the sample to the time the results are sent to the ordering physician. The best in class systems beat this 30-minute TAT goal even during times of peak processing workload. Most important, rather than having a mean of 30-minutes, the top performers have driven variation below 10 minutes.
Using Lean and Lab Automation in Microbiology at DynaLIFEDx
One lab that recently combined Lean and total laboratory automation was DynaLIFEDx Diagnostic Laboratory Services in Edmonton, Alberta, Canada. One of the largest labs in North America, DynaLIFEDx processes 900,000 microbiology specimens annually for more than 120 hospitals and health systems in Alberta, Saskatchewan, and the Northwest Territories.
When its microbiology lab combined Lean with TLA in September 2013, the lab recorded:
• Improved turnaround time;
• Reduced errors;
• Standardized specimen handling and processing;
• Streamlined operations; and,
• Enhanced antibiotic stewardship.
In addition, combining Lean and TLA helped the DynaLIFEDx microbiology lab lift productivity so much that it could handle a 15% increase in specimen volume over 18 months while also reducing staff by six full-time equivalent positions.
Lean and Automation Cut Microbiology Test TAT to Just 1 to 1.5 Days
“After the lab implemented its TLA system, the microbiology staff saw the time to report results drop from 1 to 5 days to 1.5 to 2 days,” stated Norma Page, the lab’s Vice President of Clinical Operations during a presentation at the Executive War College in New Orleans last May. “When the staff compared the number of labeling errors in one month (March 2012 versus March 2014), the number dropped from 106 out of 70,523 specimens processed (for a rate of 0.150%) to 13 errors among 77,951 specimens processed for an error rate of 0.017%.”
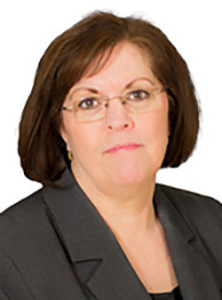
Norma Page (above) is a medical laboratory and finance professional with hands-on experience in all aspects of laboratory medicine, including testing services, patient care, systems and support infrastructure, quality management, laboratory integration, business acquisitions, and strategic, business and financial analysis. She is a registered medical laboratory technologist and holds a Master of Business Administration degree from Heriot-Watt University in Edinburgh, Scotland. (Photo and caption copyright: Dark Intelligence Group.)
Our sister publication, The Dark Report published a seminal study that confirmed the performance advantages that Lean labs using lab automation have over non-Lean labs using automation. The study was done by Thomas Joseph, CEO of Visiun, Inc., of Ann Arbor, Mich.
Working from a database that included 100 labs, 14 of which were incorporating Lean methods, Joseph determined that Lean labs consistently outperformed non-Lean labs in the important measures of average test TAT, staff productivity, and reduction of outlier test reports, despite the fact that all labs were generally using comparable automated systems for chemistry, immunoassay, and hematology.
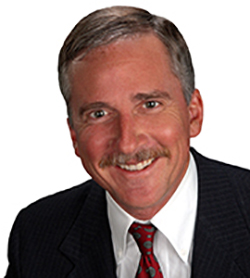
Thomas Joseph (above), CEO of Visiun, Inc., is a seasoned consulting professional with 20 years of consulting experience and areas of expertise that include financial management, operations assessment, and improvements using Lean strategies, and research and development. Joseph’s research in the area of performance metrics has led to the development of the most comprehensive database of performance metrics in the laboratory industry.
Lean Labs with Automation Sustain TAT Even with Large Test Volume
“With Lean labs, we saw that the relationship between test volume and TAT is almost flat, meaning Lean labs are managing results regardless of volume, because larger volumes have almost no effect on TAT,” observed Joseph. “What’s more, the larger Lean labs are doing just as well. The largest lab we studied did about 1.6 million annual tests and could do a routine CBC in about nine minutes. The smaller Lean labs, with annual volume of about 400,000 tests, did a routine CBC in about eight minutes. Work processes in Lean labs allow them to handle increased workload without suffering declines in TAT the way conventional labs do.” (See The Dark Report, Volume XV, No. 1, January 21, 2008.)
For all these reasons, in vitro diagnostic manufacturers have recognized the power of combining Lean with lab automation and the latest best-in-class total automation systems are designed to accommodate Lean labs. “For these systems, manufacturers incorporate Six Sigma principles into the actual automation workflow by working to eliminate bottlenecks on the automation line,” noted Ross.
Automation Solutions Should Be Designed to Eliminate Bottlenecks in Clinical Labs
“If you look at lab automation systems that don’t have a philosophy to eliminate bottlenecks, then specimens will get held up at the centrifuge or at various analyzers,” he explained. “Then, lab test turnaround times have wide variation, which physicians don’t like because it creates unpredictability in when the lab reports results to them.
“Conversely, the modules in best-in-class automation systems are designed to move at the same speed,” added Ross. “That includes the centrifuges, analyzers, decappers, recappers, and all essential components. When you do that, you start to get very consistent turnaround times because—if you have 100 samples and each sample gets loaded every three seconds—you will get results every three seconds. Therefore, your variation in turnaround is very, very minimal. When your lab does that, physicians ordering tests will see the consistency and thus the lab will see an overall improvement in its relationships with physicians,” stated Ross.
White Paper on Combining Lean and Total Laboratory Automation
To help clinical laboratories understand all the issues when implementing Lean and a total laboratory automation system, The Dark Report and Dark Daily have produced a white paper on this topic. Titled, “Buyer’s Guide for Clinical Laboratory Automation Achieving High Production Lab Automation and Lean Workflow: What Lab Managers Should Know Before Issuing the RFP,” the report can be downloaded here.
In the report, readers will find a thorough discussion of the issues related to combining Lean and TLA, along with an examination of the questions lab directors and pathologists will want to answer before they make a decision to purchase and implement a new TLA system.
—Joseph Burns
Related Information:
More Clinical Pathology Laboratories Are Buying Total Laboratory Automation
Innovative Labs Combining Lean and Automation in Clever Ways
The Economic Realities of Lab Automation
Implementing a Laboratory Automation System: Experience of a Large Clinical Laboratory